As some of you know, digital.forest was acquired earlier this year. While my payout as a stockholder wasn’t “retire now” in scale, it has allowed us to upgrade the Goolsbee fleet. First and foremost I set out to buy Sue a cruiser to help her sore back and smooth out her hectic driving schedule with something super-comfy. We test-drove a lot of mid-range machines, and she settled upon a Mercedes-Benz C300. It took me a month or so to find the right one, at the right price. She now enjoys a 2009 C300-4Matic. It is hands-down the best car we’ve ever had in the Goolsbee garage. VERY comfortable, and drives super-smooth.
This means her 2006 Jeep Liberty CRD is now for sale.
Christopher finished school at the end of the winter quarter, and is now preparing for law school. Since he loves the car and learned to drive in it, I’m giving him the TDI. It for him will be like the ’80 Diesel Rabbit I drove when I was his age – a great, reliable, frugal first car.
“How about Chuck? What does he get?”
I wanted something fun for my new commuter car. My drive to work is actually quite enjoyable – a choice of twisty two-lanes, largely without traffic. I love to drive roofless. I like to shift my own gears. (In hindsight, I’ve never owned a slushbox for *my* daily driver.) I don’t need more than two seats. I didn’t want to spend that much. I started surfing Autotrader and eBay for used cars meeting the above criteria. After filtering out the Miatas (sorry – while I know they are GREAT cars, they are also nearly ubiquitous) my searches turned up a good selection of interesting cars. MR2s. TTs. S2000s. 350/370Zs. Boxsters. SLKs. Some 911s and Corvettes. Even a Jag (Holy depreciation Batman!)
After the wonderful experience of hucking the ClownTown Roadshow’s old E30 BMW around the track now twice – with every lap bringing a grin to my face, I figured I owed a look at the Z3/Z4 line of cars. A coworker at Facebook loaned me the keys to his 2006 M Roadster while I was in Menlo Park for meetings several weeks back and halfway through the drive I decided this would be my next car.
I decided upon a color & trim choice (blue exterior, grey/wood interior) and went hunting. Autotrader turned up a few, as did eBay, but then I was referred to a car broker in the Bay Area. The idea is you tell them what you want, and about what you will pay. I knew what I wanted, and my shopping gave me an idea of what the fair market value of these cars are now, so I laid it out for the broker. He found me one in SoCal within a few days, and now the car is mine. Totally painless process. I highly recommend it over trying to buy on your own.
The car is a 2007, has ~33k miles, and is REALLY nice.
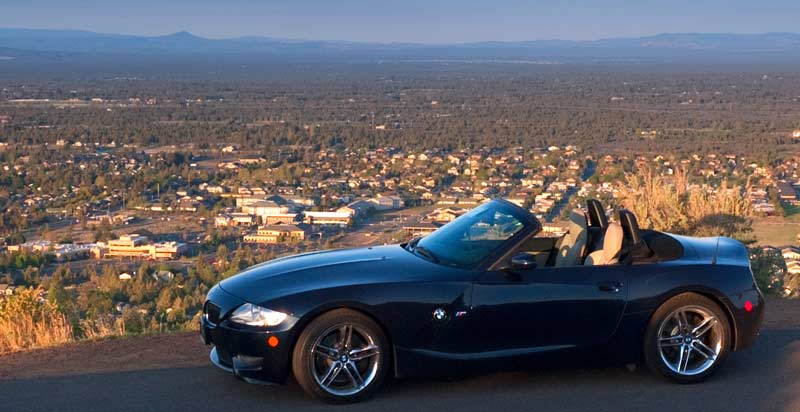
While I’m not a huge fan of the Z4 styling, the M version seems to tone down some of the more outrageousness, while upping the “ultimate driving machine” bit. It is very much a modern E-type: Classic “long bonnet, short boot” styling. Minimal interior, maximum driving pleasure. High horsepower & torque straight six. Laughable cargo space (though easily 3X what the Jag has!)
I’ve only has it a week, but every mile has been grin-worthy. The miles per gallon can’t touch the TDI, but the smiles per gallon is way past the redline. I can afford the gas now. 😉